Tailings, Waste Piles and Profits
Throughout the world there are literally
billions of tons of spent ore in waste piles dotting the landscape. Multiple millions of
dollars of non-renewable resources are lying about in huge mountains of forgotten
materials.
Companies have spent large amounts of money to locate, excavate,
size reduce and process these reserves. Some of the ventures were efficient, some of the
technologies worked and some of the operations made money.
Why is so much metallurgical value languishing in forgotten
mountains of waste?
- They did not realize they were suffering a loss.
- They were aware of the losses but were unable to alter the situation.
- They were aware of the losses but found it convenient to ignore or to
deny the loss was of any significance
- The "best" technology available was inadequate
If the best methods of the day were based on very rich reserves, or
cheap labor, or the necessity of producing metals for political reasons, then the recovery
was essentially irrelevant.
In the past world of gold mining, the reserves were mined for the
rich values leaving mountains of tailings behind. Coarse gold was recovered but microfine
gold was not. Some tailing piles have values over 1 ounce to the ton.
Many third world countries operated their metals industries at a
loss just to produce hard currency, as in the case of Peru and their copper industry. The
communist bloc, or "central planning" countries ran their metals industries to
"keep the wheels turning". Czech, Poland, Ukraine and Russia are good examples
of this.
In Poland, fairly extensive gold mining was carried on in the 1700s,
but they were plagued by "devil gold", a material that would not melt. They left
over 150,00 hectares of tailings behind. Platinum was discovered around 1800, but the
waste piles were never recovered.
When reviewing the history of metallurgical and mining technologies
there is little doubt that millions of tons of waste were declared barren when they in
fact contained large economic values. This isnt meant to criticize yesterdays miner,
because the same statement holds true in some cases today.
Some technologies were so flawed that the "West" stopped
using them in the last century while the third world held on dearly. Martin furnaces in
the steel industry and muffle furnaces in the zinc industry are good examples. Keep also
in mind the HAZARDS of turning in politically incorrect reports on efficiencies of
recovery and making your boss or the "central planning boards" look bad. In the
third world this activity could be quite damaging to your health.
Another thought to ponder is the alteration of materials over time.
Chemistry provided by the forces of nature over long periods can and will alter materials.
As temperature and moisture levels change within a pile, the pile breathes. Oxygen,
hydrogen and nitrogen migrate to the voids. Gases generated within the heap migrate and
are modified or expelled. Each rainfall brings a new charge of acids, which continue to
alter the minerals. The products of decomposition generate soluble salts that attack other
minerals. The metals values may be recoverable now.
The piles are modifying everyday, very slowly, but ever changing.
Todays technologies recovering yesterdays wastes. Wastes
that are already excavated, size reduced, accessible, of known composition, and a blot on
mans record of environmental stewardship.
The possibilities are quite exciting! The possibility for
environmental remediation is enormous!
With this said, we introduce the CDE FAMILY of leach recovery
technology. A non-cyanide leach that removes any metal or metallic residue from any media
including toxic or hazardous waste. CDE leach liquors will digest and surrender any metal
from antimony to zinc.
A Leaching Primer
Suppose you had a bucket of salt and sand mixed together that you
wanted to separate. One method could be individual grain separation by hand. This would
work but not very effectively.
Consider then a leaching method using water to dissolve the
salt and removing it in liquid form. The liquid could then be evaporated and the salt
recovered in solid form. This method would be more efficient, and is a very simple
materials recovery method utilizing leaching.
Therefore, for our purposes, leaching is the method of dissolving
desired metals for the purpose of recovery, remediation and/or separation.
Water will work on salt but certainly not on metals. The problem is
(was) finding a leach to digest or dissolve the metal(s) contaminants. Ancient Alchemists
quested for the universal solvent but once they found it they to find no container to hold
it.
CDE leach liquors require non-metallic containers.
We now introduce our version of the universal solvent. These leaches
have successfully digested every metal and metallic waste that it has been exposed to.
CDE 2 Leach
CDE 2 leach:
- Is an aqueous base formulation of common materials that combine to
create an extremely aggressive method to dissolve, or "digest" metals.
- Has an initial 0 pH value.
- Has an initial ORP (oxidation reduction potential) in excess of 700
mv
- Has been independently evaluated by one of the most respected mine
labs in the USA. KD Engineering Co., Inc in conjunction with Metcon Research, Inc did a
cyanide/CDE 2 comparison study for gold recovery. Their conclusion was that CDE 2
recovered 6% more gold than the cyanide.
- May be formulated in the field by technicians with only rudimentary
experience.
- Replaces cyanide methods of gold recovery. Cyanide is extremely
dangerous to site personnel and the environment. It is an archaic methodology that has no
place in todays world now that there is a better solution.
- May be modified to selectively "leave", or not digest
certain metals so extremely complex ores can be "simplified". An example would
be a silver-bearing ore with a high content of base metals. The host ore can be treated so
the base metals dissolve in solution leaving only silica and silver behind. Graviometric
separation can then be employed for low-cost separation of the silver.
THE COLOR OF
MONEY
These are the particular colors that
specific metals become when dissolved in my leach.
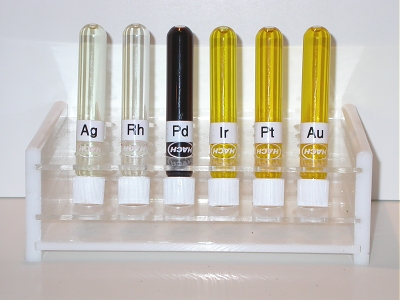
THE LEACH SYSTEM
Mr. Paul Jones developed the leach system
in lab and field trials over the past twenty years. The initial intent was to develop a
solution that could be used in the field to determine on-the-spot analysis of metal
content in rock. Along with a great deal of experimenting in the mining industry, Mr.
Jones finally produced a product that not only works for exploration purposes, but also
all metals mining situations.
The leach is inexpensive to produce and can
be made almost anywhere. With a pH of 0 it is one of the most corrosive chemical
compounds known. The unusual nature of the leach is that it is also buffered against all
organic material rendering it safe to use and enabling safe disposal.
The single most important element of the
hydrometallurgical method of removing metal from ore is to be able to get the metal in the
ore into solution. Once in solution there are different ways to extract the metal. The
system has been designed to selectively remove the dissolved metals with the use of
designer resins. The designer resin industry has been extensively developed for the
hazardous waste industry. We have found it to be an excellent, efficient and reliable
method for removing the metals from our pregnant solution.
Once the metal has been extracted from the
leach solution the remaining leach fluid can be reintroduced to the digestion circuit and
recycled over and over again. The environmental impact of the leach residue in the
tailings is negligible and contains no harmful chemicals.
This system requires no heat and no
pressure in order for effective operation in a mining facility. This allows for
construction of a commercial plant at fraction of the cost of hydrometallurgical or other
installations. The cost of ongoing operations in a plant would be significantly lower than
other systems. Also, the construction time and effective maintenance of the plant would
increase bottom-line profits for any company utilizing the system.
The overall effectiveness of the leach
system provides answers for many problems in the processing of most metals.
Included is a report from a major lab that
ran independent tests and analysis on the leach. The conclusions attained in this letter
verify the above statements.
To View
Independent Test Results, Click Here
Leach Plant Flow Chart
- General
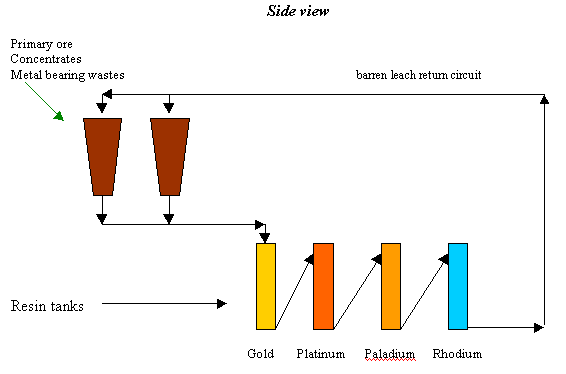
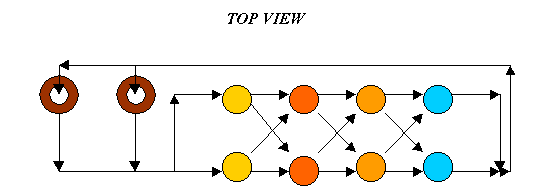
|